The Pro’s & Con’s of Modular Buildings
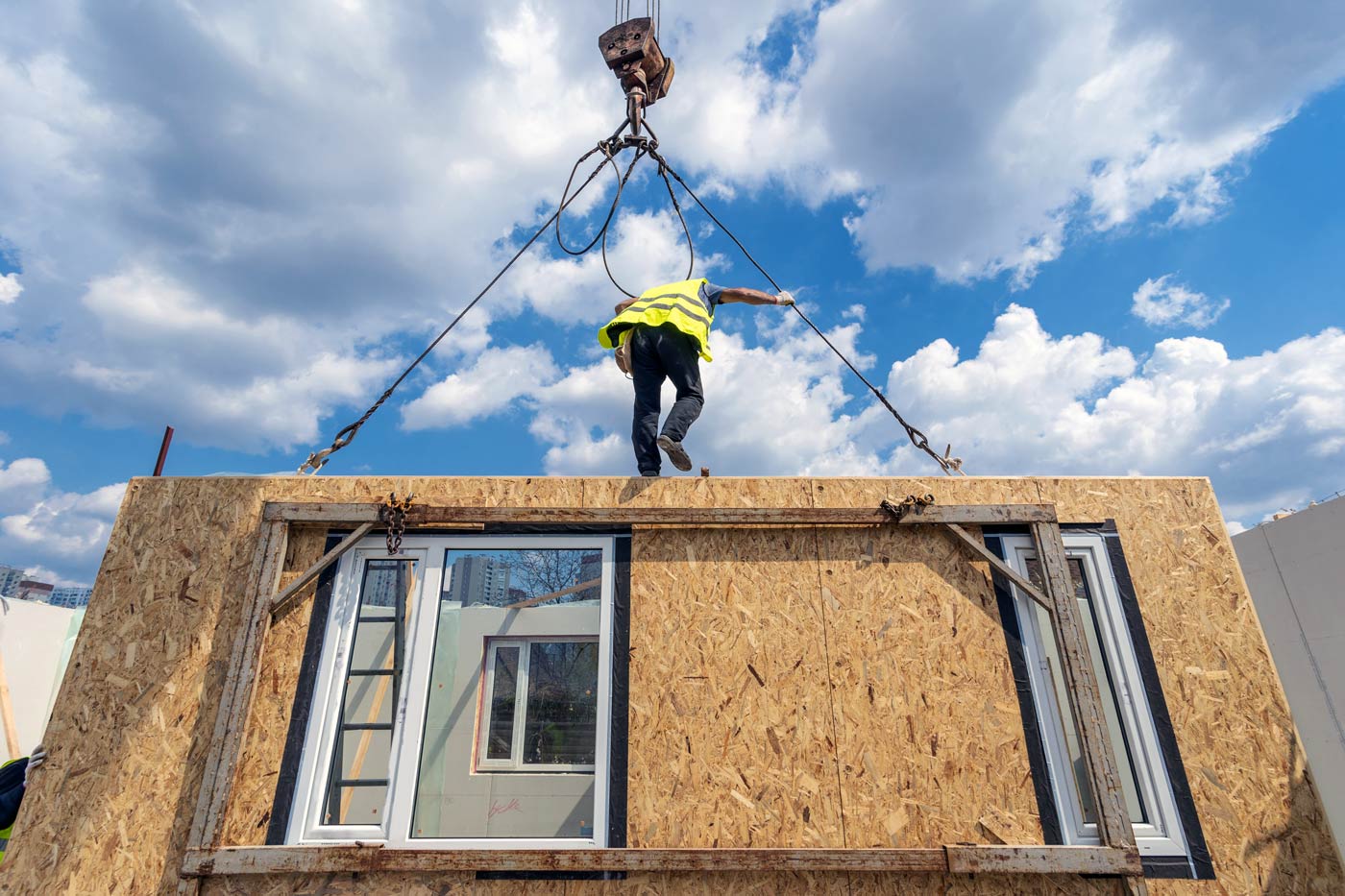
Modular buildings are becoming a popular option for potential homeowners who want to build their own homes rather than buy a pre-existing home or build a stick-built building.
And there are a lot of pros and cons to wrap your brain around for both options.
We’ll be going into the benefits and potential drawbacks of both styles, but before we do, it’s important to cover a few of the most common questions for modular building.
Question #1: Are rigid frame buildings also considered modular?
Modular Buildings vs Rigid Frame Buildings
Modular buildings and rigid buildings are quite different.
Modular buildings are built in modules, or components, in a factory setting. These buildings are designed to meet strict codes, and each module is installed to form one structure.
Modules are transported to the building site, but completed modular buildings are not.
Modular buildings aren’t the same as portable buildings that are often used in schools and warehouses.
Rigid frame buildings are made with I-beam main frames. Strong and durable, these building’s resist deformation and are best for:
- Low-rise buildings
- Clear span framing
Rigid frame buildings can be high rise buildings, and some of the world’s largest buildings use this form of building because of its versatile design and strength.
Where Are Modular Buildings Being Used?
Modular buildings are popping up everywhere, including:
- Commercial buildings
- Apartments
- Dorms
- Residential homes
Modular buildings are versatile, and they can be used to construct churches, commercial buildings and even apartments in a shorter time span and at a lower cost.
Small additions to buildings are another great option for a modular building.
Where Are Rigid Frame Buildings Used?
Rigid frame buildings are versatile, and they’ve moved away from the metal box look that people used to associate them with. Now, rigid frame buildings are used for:
- Warehouses
- School gyms
- Indoor arenas
- Residential homes
- Hotels
- Skyscrapers
And the ability to customize the building means that it can be transformed into the client’s exact solution.
How Are Modular Buildings Transported?
Modular buildings are made in a factory, so they need to be transported to their final destination. Transporting these buildings requires each module to be transported individually, and then the final building is assembled on-site.
The majority of the work is completed in the factory, greatly reducing the building time.
Commercial trucks haul the modules to the final site.
You’ll often see parts of these buildings making their way down interstate highways. State laws dictate the limitations on modular buildings. State transport laws have width restrictions for modular modules, so it’s important that the constructed module meet these width restrictions.
It’s a safety measure that keeps drivers safe on the road.
In general, the average width will be 10′ – 15′, but it does vary from state-to-state. When transporting a module over state lines, the module must meet the standards in multiple states, which further complicates the transport process.
Modular Buildings Benefits
If you’re considering modular buildings, you’ll find that there are a lot of advantages to this building type. Modular buildings offer:
Fast Construction
Since a modular is built in a factory, construction is much faster. Weather doesn’t get in the way of a construction company’s work, so there are no delays in the process. You don’t have to worry about the home being exposed to the elements.
Illness of laborers is also less common.
Modulars are put together on-site, so it’s a very easy process that doesn’t include the same level of difficulty as building a home on the site.
Affordability Options
Of course, since the home is built faster and with fewer complexities involved, the price is adjusted. Yes, there are different pricing levels because of customization, but when a stick-built and modular of the same construction is compared, the modular is often less expensive.
You’ll want to compare the costs between builders, and you’ll also want to consider the local market.
There are different options everywhere, and even when the cost is comparable or on-par with a stick-built, modular often exceeds local standards and building codes. The overall construction of a modular is often better and exceeds that of a stick-built home or building.
Energy Efficiency
There’s a high level of efficiency with modular buildings. These buildings offer state-of-the-art windows and doors that seal in heat or cool air. The tight seams allow for lower overall energy costs and much higher energy efficiency levels.
Natural disasters are also able to be withstood thanks to the tight seal that modular buildings offer.
There’s also a much lower carbon footprint when making a modular build. The waste is less, too, since it’s easier to control all of the variables that go into the building processes. Less waste makes the modular building eco-friendlier while also having a very high energy efficiency.
Foundation Homes
Mobile homes are different than modular homes despite many consumers assuming that they’re exactly the same. Modular homes go into a foundation, and this makes them as strong or stronger than a stick-built home.
Mobile homes cannot meet the same level of durability and strength of a modular home.
Some also offer steel frame construction, which allows the building to be much more durable and able to withstand the elements compared to other building methods. Overall, modular buildings are great for:
- Affordability
- Energy efficiency
- Fast construction speeds
Modular Buildings Cons
Modular buildings are not without complaints or issues. Every building method has its own pros and cons, but it’s important to know and explore the cons of these buildings before purchasing. There are a few cons to know about:
Upfront Payment of 20% on Average
Modular homes do not offer the same, low upfront payment as other home building or mortgage options. You’ll find a lot of no-money-down or low-money-down options when buying buildings or homes.
But modular homes or buildings are being built from the ground up.
When building a modular, it’s common to get a construction loan that will then move into a permanent loan. These loans may require 20% down before the construction process even begins. There are also construction loans that will need to be paid in installments.
The higher upfront costs will lead to lower interest over time, so this is something to consider.
Borrowers will need to locate lenders that are willing to provide construction loans. A lot of lenders will want a substantial down payment. It’s important to also consider a construction-to-permanent loan, which will save the borrower money on closing costs.
Land Costs Can Be Expensive
The cost of land may be expensive, so you’ll need to have an allowance for the expense of the land. There’s also a lot that goes into the land before a building can be built. You’ll find that there are a few hurdles along the way, like:
- Soil testing
- Clearing land
- Building a driveway
- Water
- Sewer
- Electricity and utility hookup
- Inspections
- Permits
All of these factors need to go into the ultimate price of the modular building. It’s definitely an expense that needs to be considered versus buying an existing structure. With that said, a lot of the above expenses will also be part of building a home of any type.
There is also the option of buying land that is already clear and has utility hookups available.
Utility Hookup Concerns
The final disadvantage ties into the land issue. When you build any structure, it’s a far more complicated process than buying an existing structure. The ground will need to be cleared and leveled.
Foundation needs to be poured, and a professional will have to dig a well to find well water.
A lot of the details will need to be taken care of by the owner of the structure. There are prefab companies that will take care of all of these details to ensure that the road to building a modular is as seamless and easy as possible.
Modular or prefab buildings take a lot of the work out of building a home, but there are always hurdles involved. Lenders will be more stringent in their requirements for loans, there are land costs and utility hookup will remain a concern.
It’s a longer process when trying to build a modular building, but these buildings often come with top-tier features and warranties.
When compared to building a stick-built structure, modular buildings will be a much more affordable, effective option in most areas. The biggest concern is transporting the building to the final destination and ensuring that the building width meets local standards. Land clearing and prep is also a major concern, but with the proper budget, these concerns are common for all structure building.